



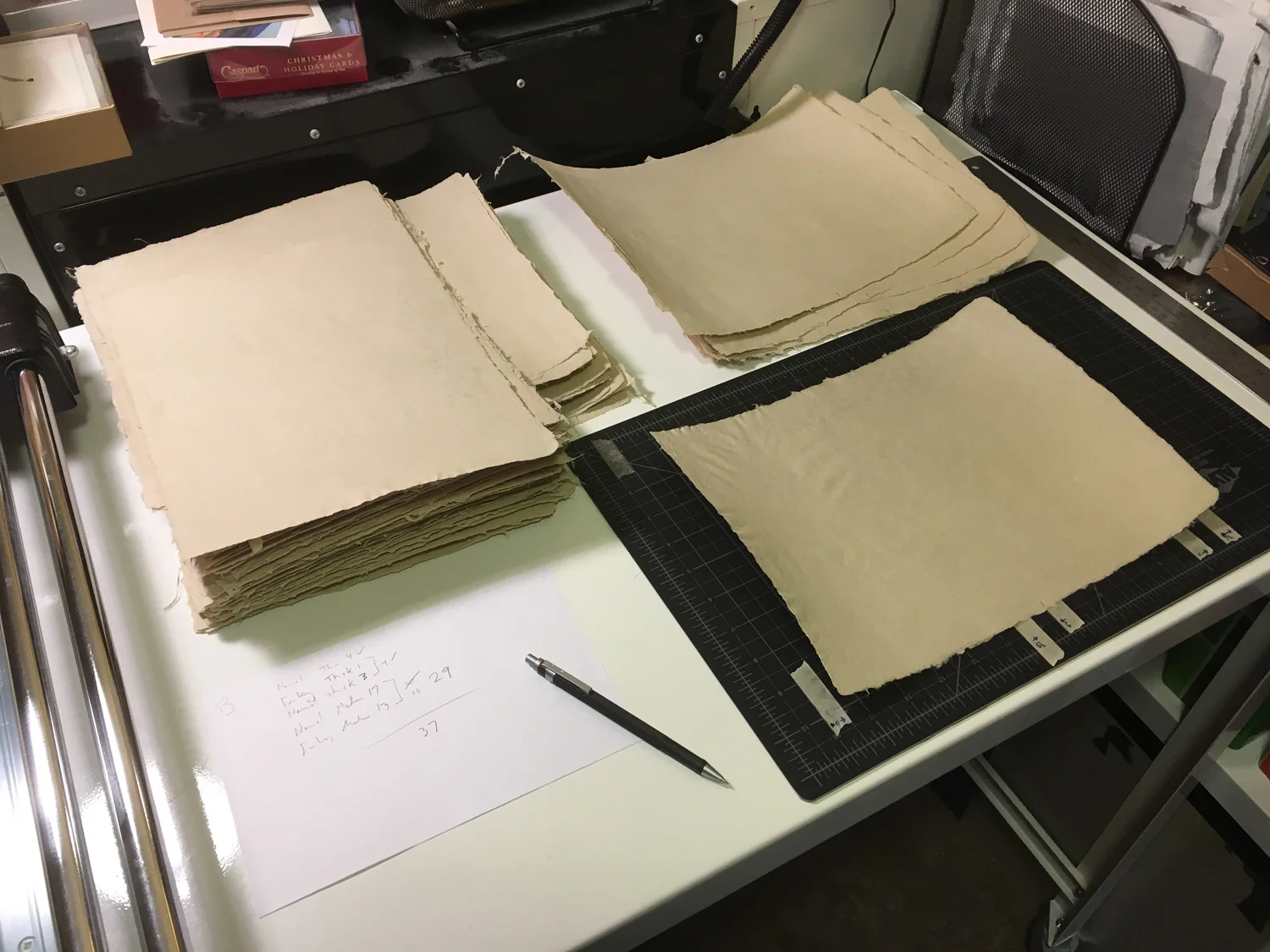
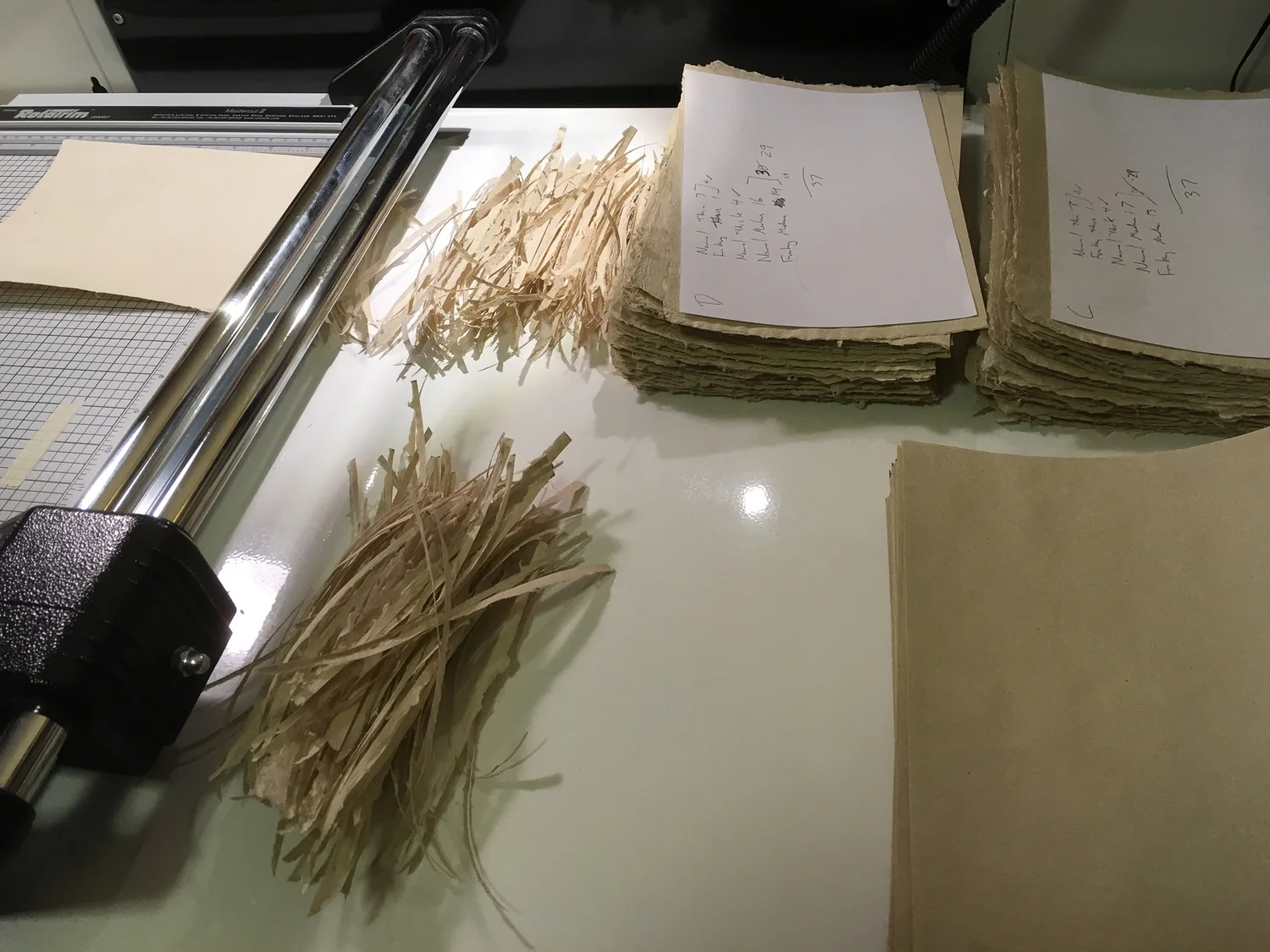



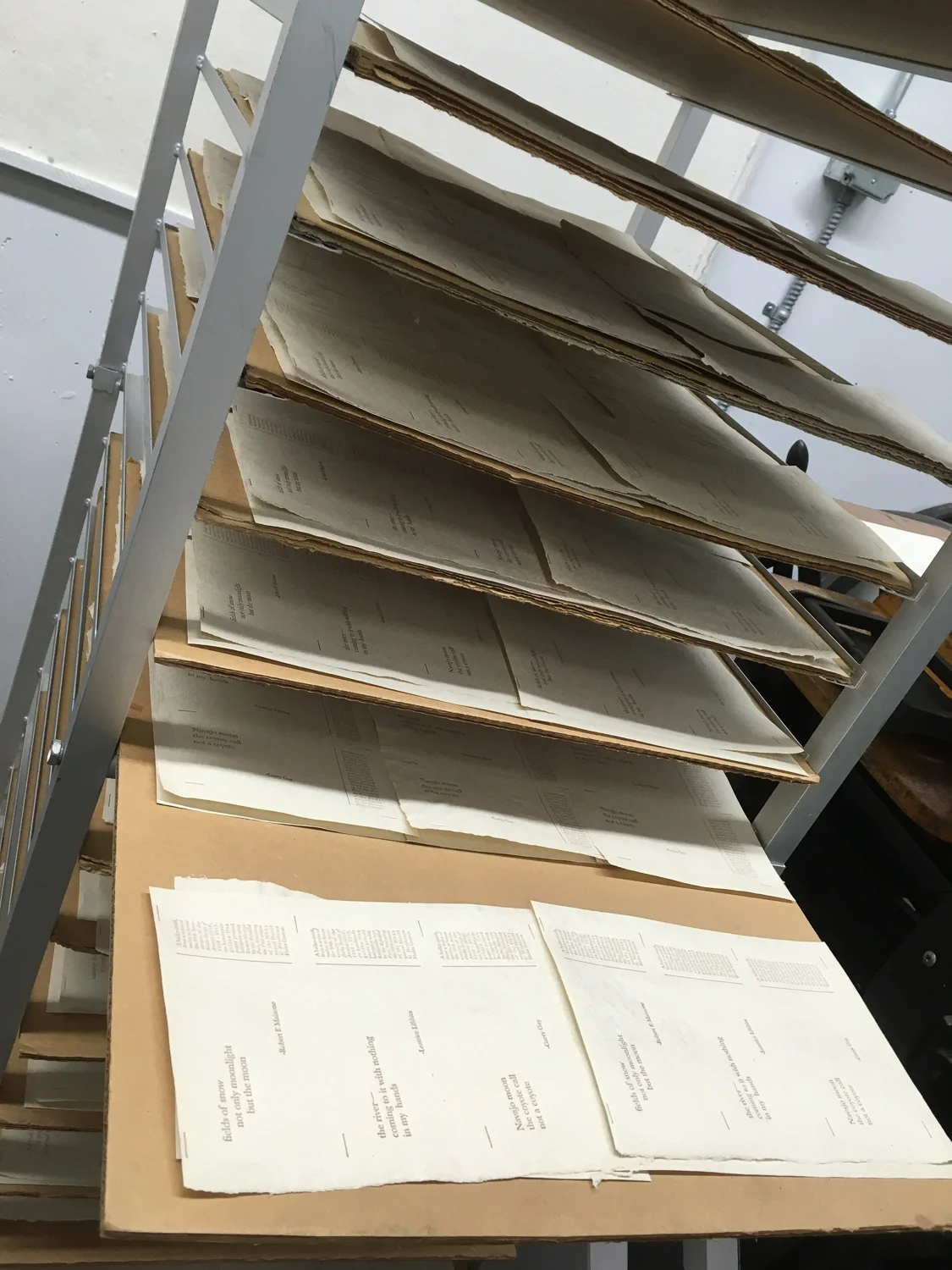
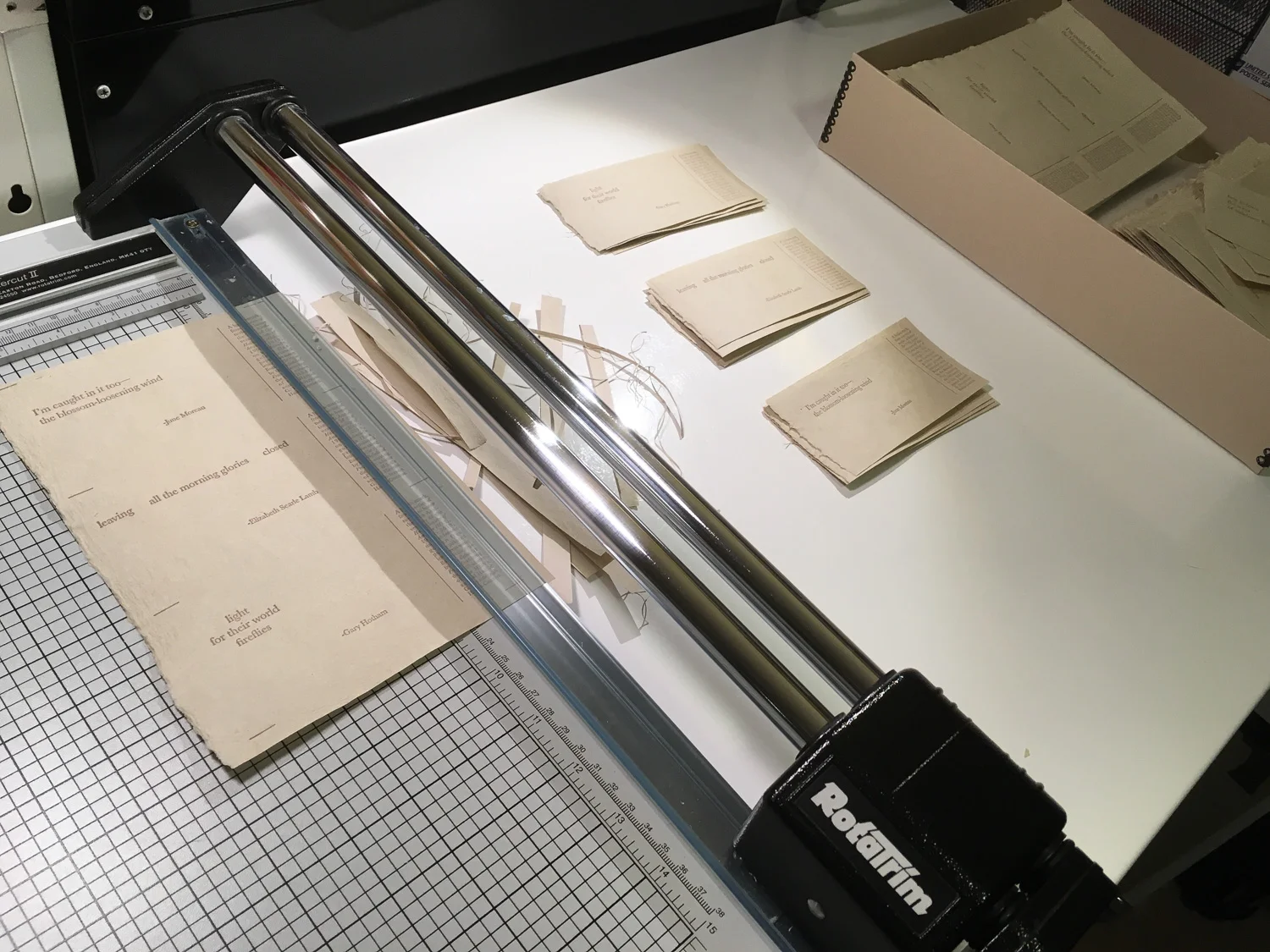

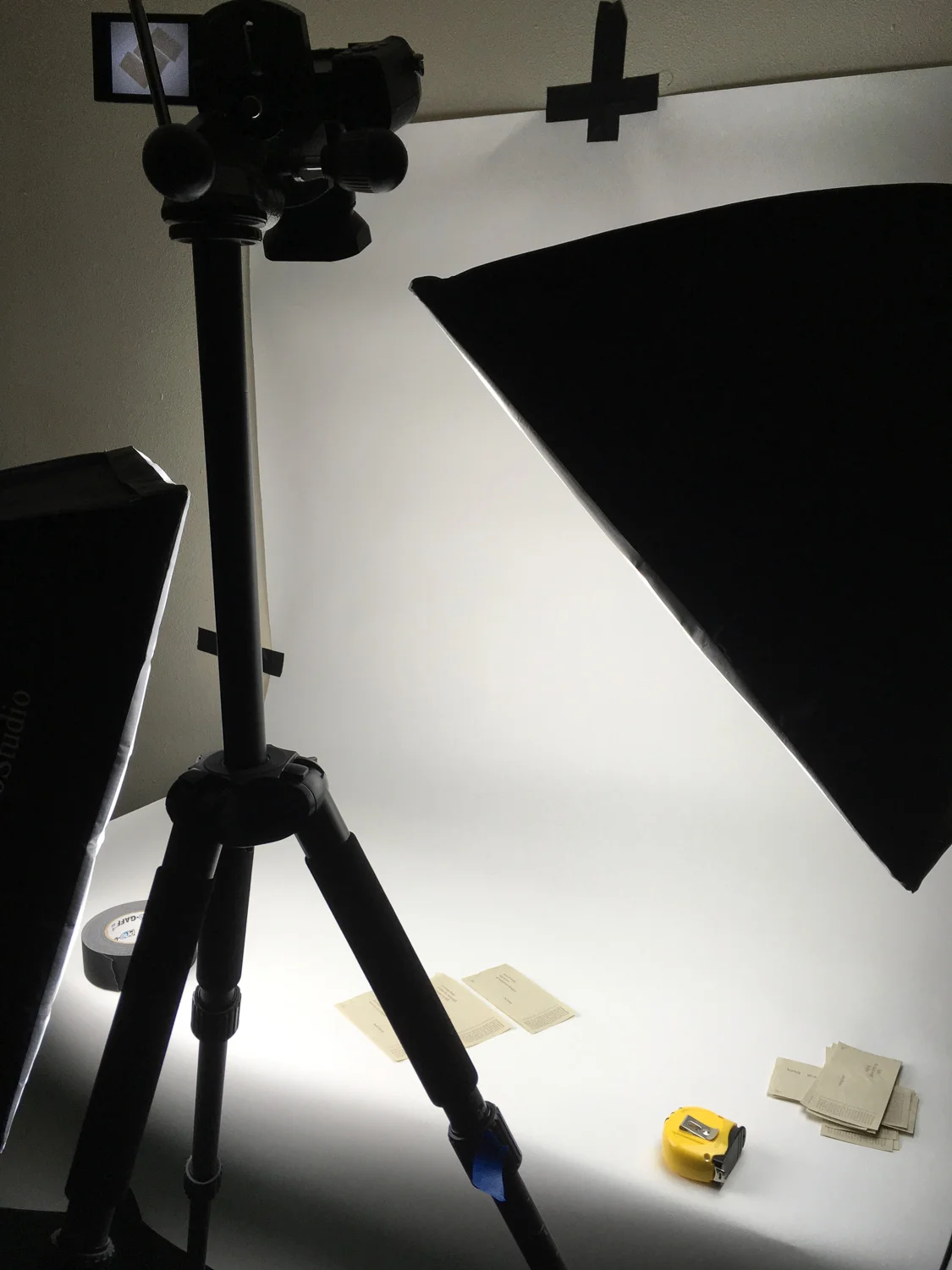

Letterpress printing began in the 1450’s with a wine press and movable type. While the presses have evolved, the basic premise of type, pressure, and ink continues into the 21st century. Note the 1568 woodcut by Jost Ammam.

The biggest benefit of the 21st century is the ability to test layouts digitally and to see what they look like in laser printed mockups. Note the array of layouts with small differences.

Layout software allows for visualization of multiple ideas and to use an array of fonts or typefaces beyond what one might have in stock in metal type.

Letterpress printing can use a wide range of papers, but in the present project, we are using 148 sheets of handmade golden flax paper.
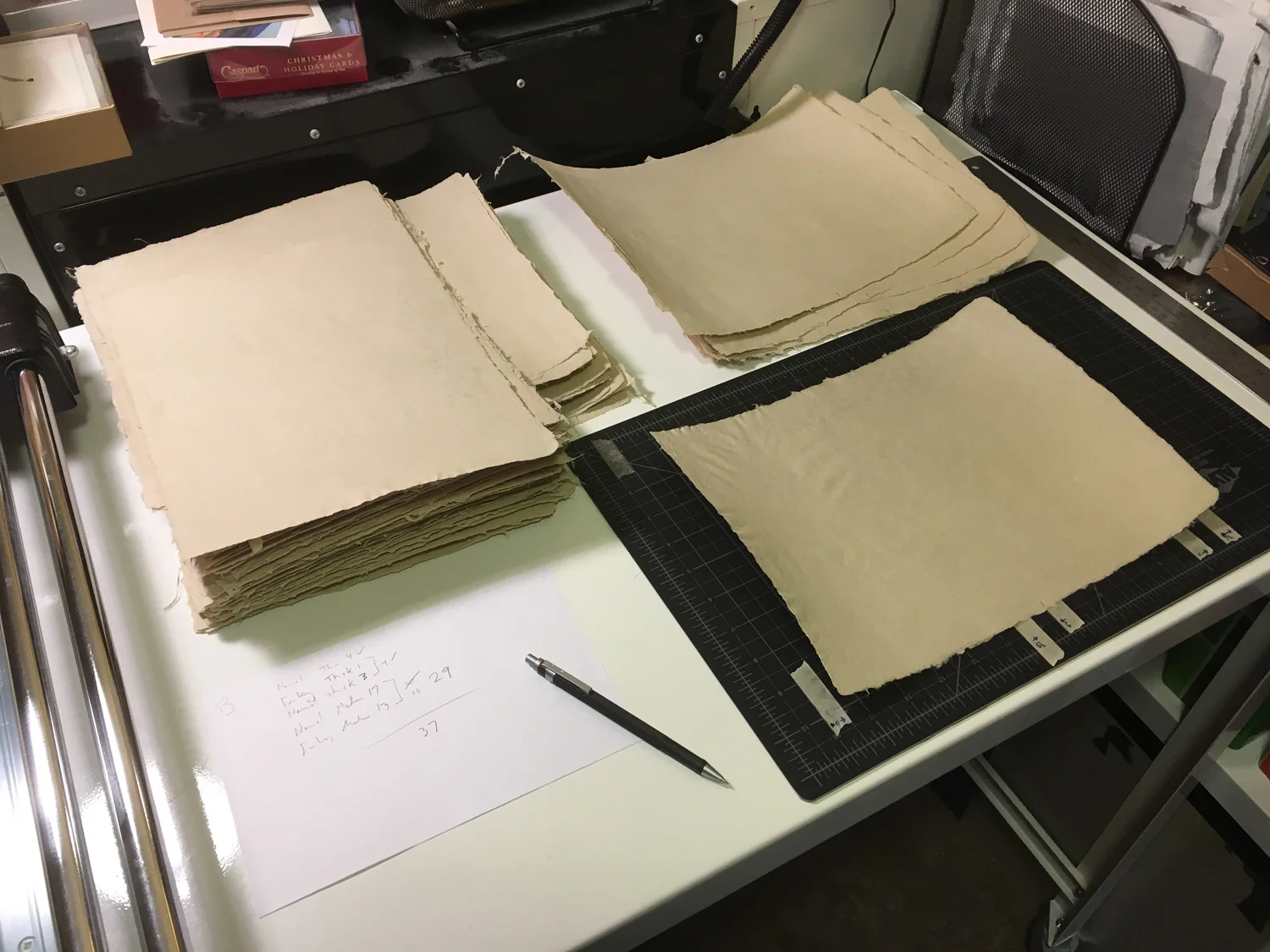
With handmade paper it takes time to go through the sheets to eliminate any that have issues. It is also important to separate them into piles based on thickness so that printing can be more effective.
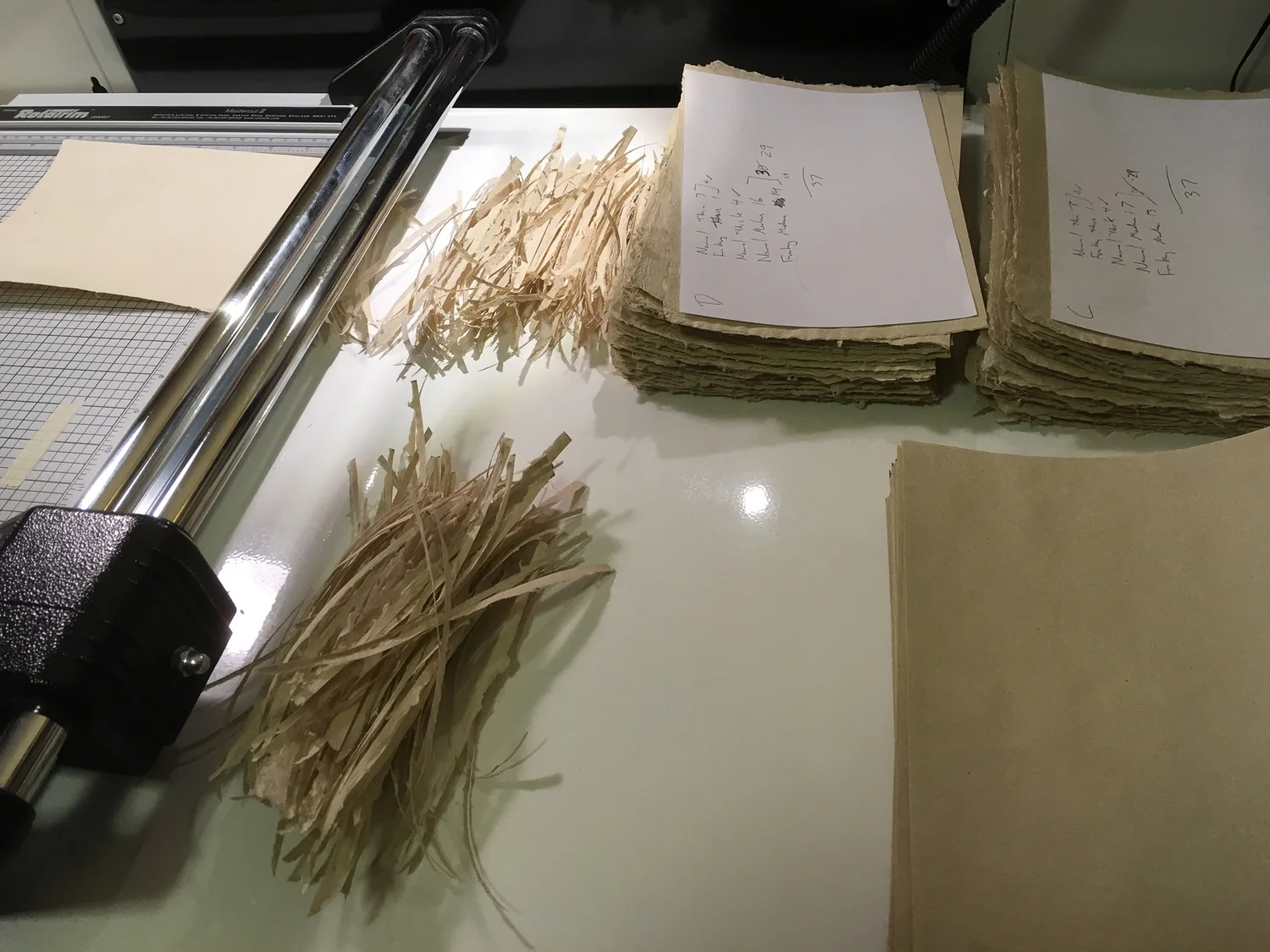
Handmade paper has four deckled edges. To make printing consistent the sheets were cut to remove a deckle. They were then cut again as each print would only be taking up half of the sheet.

The digital designs were turned into flexible plastic printing plates. This plate was secured to a printing base on a press for printing. Three prints would be made at a time and cut apart later.

Printing was done on a Vandercook Proofing Press, manufactured in the 1950s. One sheet is printed at a time.

The paper is in the “grippers,” the brown ink is on the rollers, and the plate is on the block.
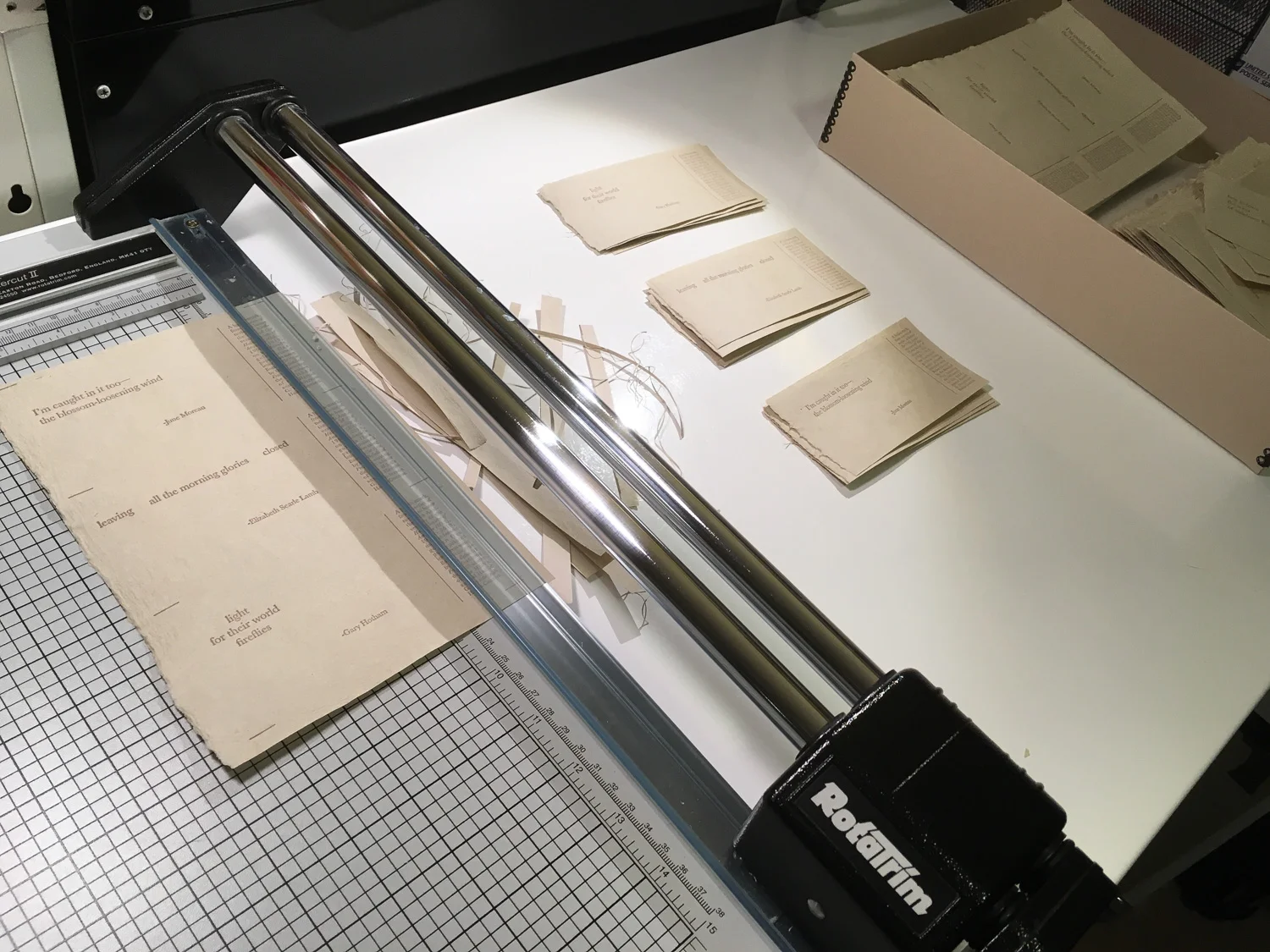
As each print consisted of three designs, the sheets needed to be cut down into their individual broadsides.

The final stage is going through the prints and selecting the final edition of 50. Any prints that have issues are left out and are considered “artist proofs.” The edition is then numbered.
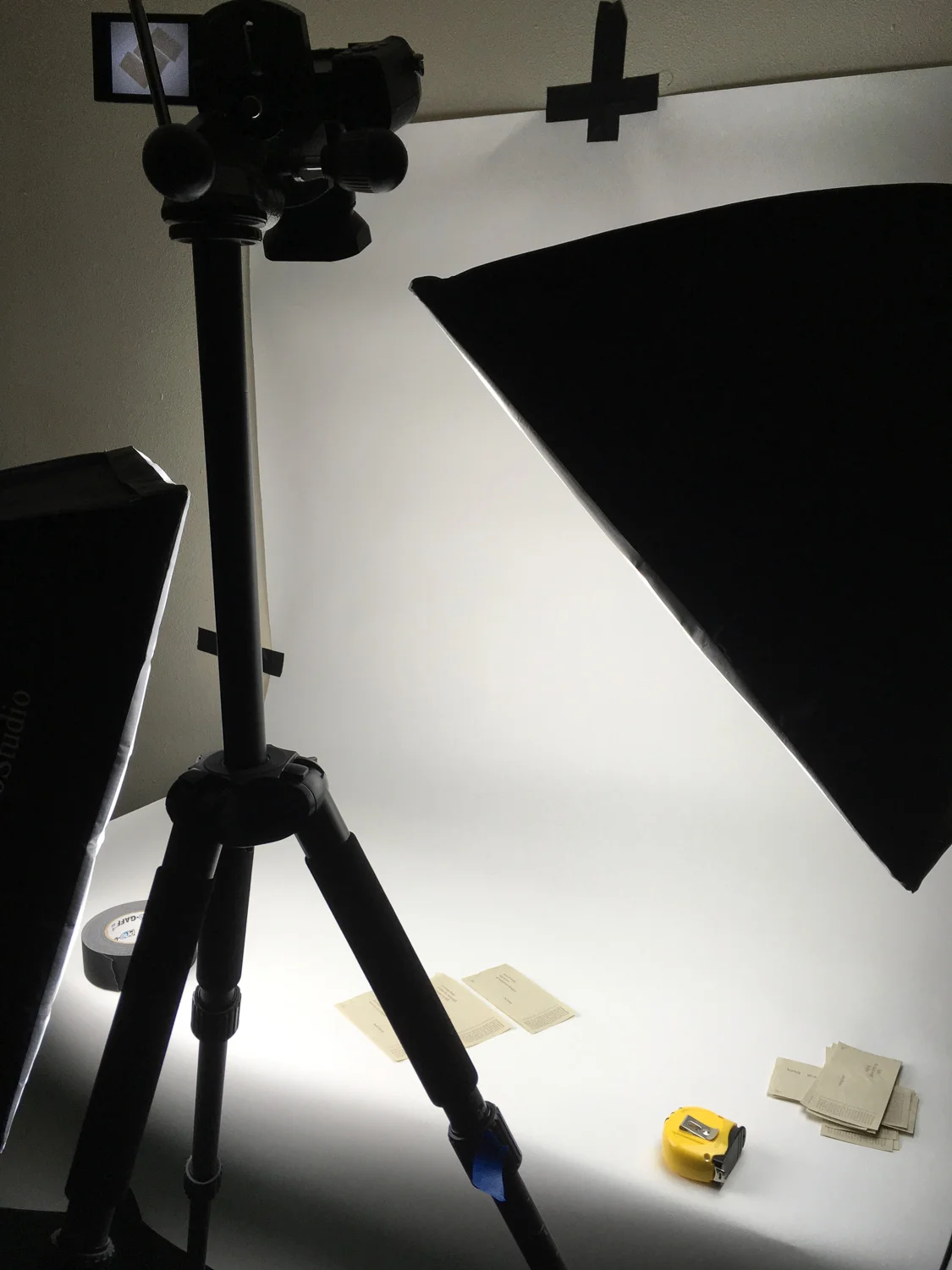
Of course, after the prints are done they need to be documented so they can be shared in the virtual realm.